Factors that impact thruster efficiency
Using the input power rating as the deciding factor for the right thruster model might leave you with a severely underrated system as there are vast differences between input power and actual thrust output from various manufacturers.
When we talk to customers about thruster size, we are often asked to offer thrusters according to electric or hydraulic motor power rating (kW). However, there is a reason why thrusters are called thrusters. What pushes the boat sideways is thrust rated in kilogram-force (kgf) and not motor power measured in watts.
The motor is only one of the components of a thruster that significantly affect the system's efficiency. Four main factors translate motor kW to actual thrust at a specific tunnel diameter:
- Motor and system efficiency
- Gear leg design
- Propeller performance
- Hydrodynamic efficiency of the tunnel installation
Motor and system efficiency
Hydraulic motors
Unlike electric thrusters, hydraulic thruster systems are more complex in regard to efficiency. It ultimately depends on all the individual components in the complete hydraulic system and how these work together.
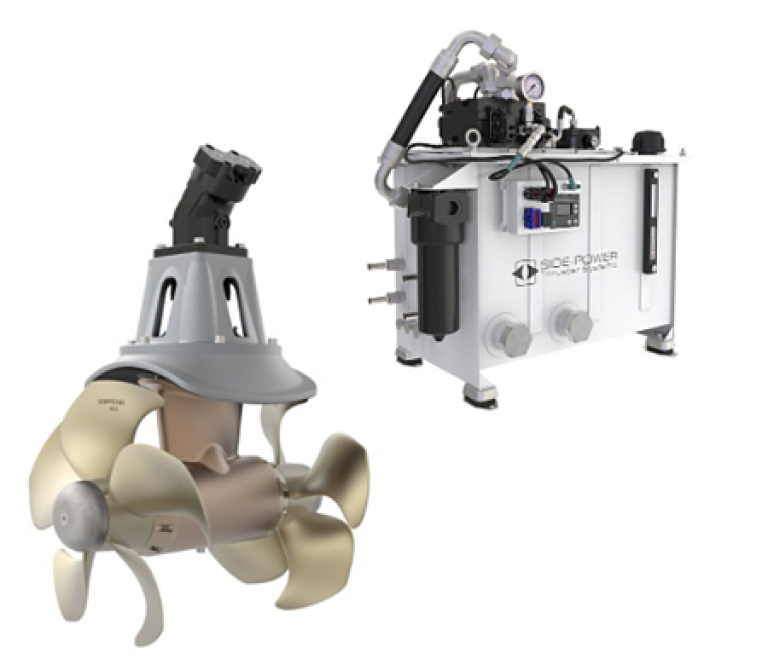
As an example, some cast iron gear motors with low volumetric efficiency (75-80 percent) will show a significantly higher power rating than a much more efficient bent axis piston motor (92-97 percent) at the same thrust level. Overall, power consumption is also affected by system design and other components like hydraulic pumps, valves, and piping. Even oil cooling- and filtration system design can influence overall performance. In a traditional, low-efficient hydraulic system, only 25-50 percent of the energy that the pump draws from its source will do any actual work, meaning generate thrust. Efficient use of the energy available in the boat is always a top priority. That is why choosing the best possible components and system engineering to achieve minimum system loss is imperative. A well-designed hydraulic system should typically deliver at the thruster propellers 70-75 percent of the energy that the pump draws from its source.
AC motors
AC motors are used with thrusters ranging from about 240 kgf and upwards. AC solutions with any voltage and, in combination with variable frequency drive (VFD), is a very efficient way to power a thruster.
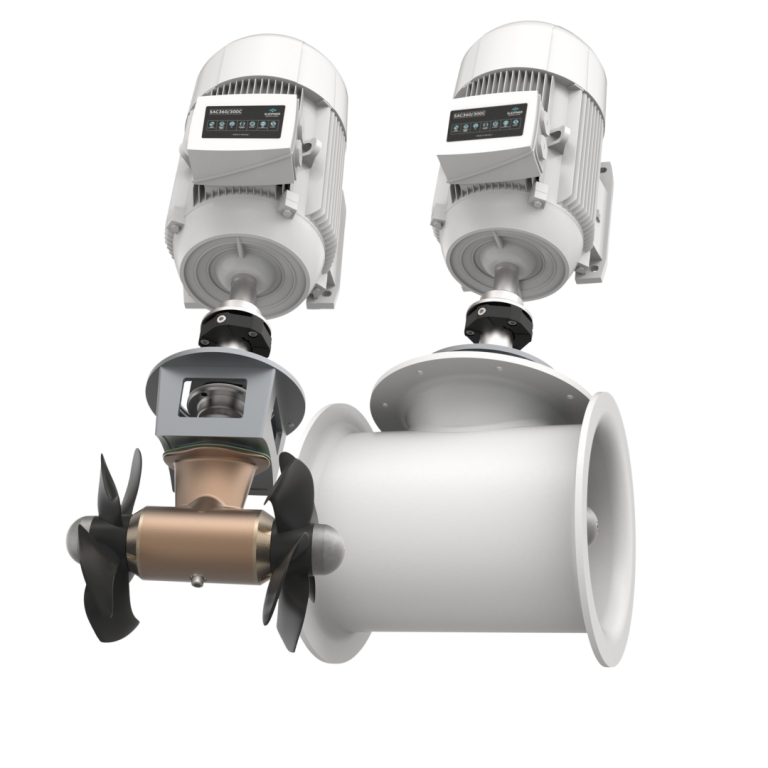
The electric power is supplied from the generator to the VFD and from the VFD to the thruster motor. In such a setup, total efficiency is typically around 85-90 percent. Most AC thrusters are available with proportional speed control. The VFD controls ramp time, RPM, and maximum current draw according to input from the thruster joystick. This way, peak loads are much better controlled and do not overload the generator, while AC on/off solutions may generate a 7x higher start-up current than the nominal current.
For context, Sleipner thrusters up to 700 kgf of thrust use high output, compact aluminum motors, with optimized windings for low weight and reduced dimensions. An additional feature is a temperature sensor installed in the motor windings. With cold feedback, the thruster can optimize for best performance with lower weight and reduced dimensions.
As a result, compared to a traditional cast iron AC motor, Side-Power thrusters can obtain up to 45 percent weight reduction. All Side-Power AC thrusters can operate in continuous duty either with full performance version "C" or limited performance when the motor temperature reaches a specific limit version "I."
DC motors
DC motors are used with thrusters ranging between 20 and 300 kgf. The power delivered to the thruster propellers depends on the voltage level in the system. High-quality components like properly sized power cables, main switches, fuses, and fuse holders cause a minimal voltage to drop between the battery and the electric motor. However, we still must consider an inevitable loss. Such a suitable 12 volts (24 volts) setup powered from high CCA-rated batteries in good condition should give minimum 10,5 volts or 21 volts in a 24 volts system on a thruster motor. That is why serious manufacturers calculate the thrust at 10,5 volts (21 volts), based on actual performance in the boat, rather than theoretical values at nominal battery voltage. It is essential to be aware of how the thruster performance data is measured so that the system doesn't end up being underpowered by calculation from unrealistic performance figures.
Leading manufacturers uses custom-developed motors with high-quality materials and components to ensure superior current conductivity and mechanical performance, which translates into maximum efficiency possible with brushed DC technology.
Gear leg design
Gear leg build quality, hydrodynamic properties, and the space it occupies in the tunnel will also significantly influence thruster performance. Using hardened spiral-cut gears is one solution to minimize footprint and achieve a compact gear leg design. The design needs to be hydrodynamically optimized and use a minimum space in the tunnel, which allows for better and smoother water flow. Compact, streamlined gear-leg minimizes water resistance and reduces cavitation, which also impacts sound levels. More efficient water flow and less cavitation mean more thrust from each kW input power.
Propeller performance
There are thruster-propeller designs on the market. To give you an example of how the impact of design can have on performance, I will use Sleipner's Q-prop.
Previously, Sleipner used a four-bladed propeller that was highly efficient. As the focus on noise level grew for our buyers, our engineering team started to test a wide range of new designs that aimed to keep the high efficiency, while decreasing the noise level. Two years down, and a thousand tests later, the result was a five-blade unique skew propeller.
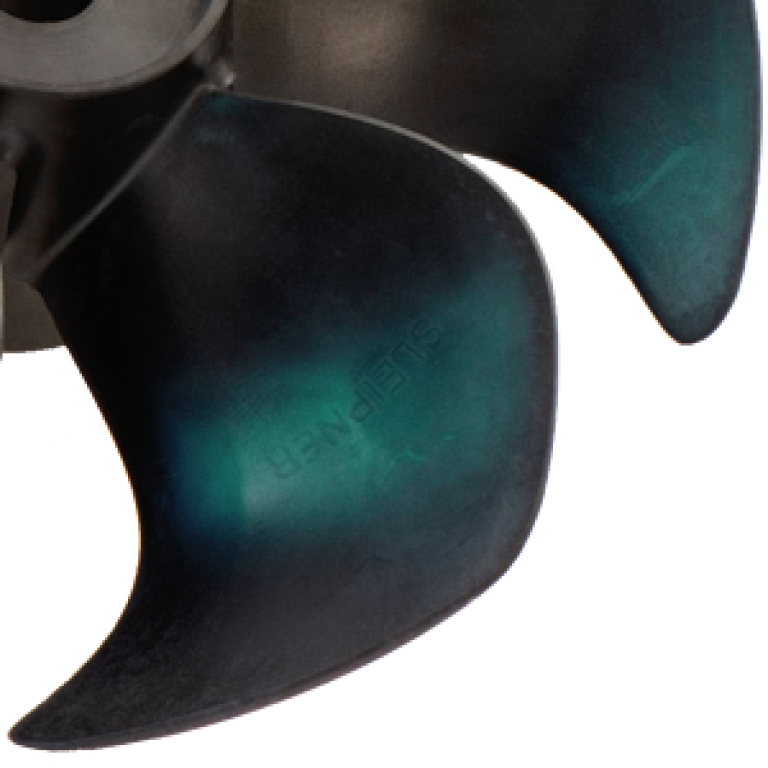
The Q-prop is designed to reduce the noise level while maintaining exceptional efficiency of the four-bladed propeller.
- Q-prop give up to 75 percent noise reduction measured in controlled environments
- Q-prop give an average of up to 40 percent noise reduction on actual installations
The Q-prop design has proven so effective that thrust levels even increased (by about five percent) on some thruster models.
Hydrodynamic efficiency of the tunnel installation
As a boat builder or installer, knowledge about optimal tunnel installation is crucial to achieving a well-performing thruster system.
Tunnel installation has a significant impact on overall thruster efficiency and noise levels. An inadequate tunnel installation will significantly reduce actual thrust output and create a lot of cavitation in the tunnel, leading to much higher noise levels.
Although this is described in detail in installation manuals, we have developed a design guide to tunnel installations that give professional installers an excellent theoretical foundation about how tunnels should be built to obtain maximum thruster performance and minimize noise level. Information about tunnel location, tunnel length, and tunnel openings are an essential part of the installation to ensure the most effective thrust out of the available motor power.
Conclusion
As you have learned throughout this article, it can be directly misleading to use the theoretical motor rating to decide which thruster model is the best choice for a specific vessel. There are considerable differences between various manufacturers on how efficiently they can convert input power to actual useful output thrust.
When comparing details other than motor power rating with different thrusters available on the market, you will find that you can often save space and cost using smaller but equally performing thrusters when choosing high-efficiency models and enjoy the extra power.